Introduction
Diesel generators play a critical role in ensuring reliable power supply in various industries, commercial establishments, and residential settings. These robust machines are designed to provide backup power during outages or as a primary power source in off-grid locations. However, like https://www.lkpowerplant.com/product/30kw-3-phase-water-cooled-diesel-electrical-generator/ , diesel generators require regular maintenance to operate efficiently and reliably. While scheduled maintenance is essential to keep generators in optimal condition, unscheduled maintenance is equally important to address unexpected issues that may arise. This article focuses on the importance of unscheduled maintenance for diesel generators and provides a comprehensive guide to effectively managing and addressing unexpected maintenance needs.
Understanding Diesel Generators
Before delving into the specifics of unscheduled maintenance, it is essential to understand the basic components and operation of diesel generators. A diesel generator is a combination of a diesel engine and an electric generator that converts mechanical energy into electrical energy. The diesel engine drives the generator to produce electricity, which can then be used to power various electrical loads.
Diesel generators are commonly used in applications where a reliable power supply is critical, such as hospitals, data centers, manufacturing plants, and construction sites. They are preferred for their durability, efficiency, and ability to provide continuous power for extended periods. Diesel generators come in various sizes and configurations to meet different power requirements, ranging from portable units for residential use to large industrial generators for commercial applications.
Importance of Unscheduled Maintenance
Scheduled maintenance involves routine tasks such as oil changes, filter replacements, and inspections that are performed at regular intervals to prevent breakdowns and ensure optimal performance. While scheduled maintenance is essential for the long-term health of diesel generators, unscheduled maintenance is equally crucial for addressing unexpected issues that may arise between scheduled service intervals.
Unscheduled maintenance, also known as reactive maintenance or breakdown maintenance, involves repairing or replacing components when a generator fails unexpectedly. Ignoring unscheduled maintenance can lead to prolonged downtime, costly repairs, and potential damage to other parts of the generator. By promptly addressing unexpected issues through unscheduled maintenance, operators can minimize downtime, prevent further damage, and ensure the continued operation of their diesel generators.
Common Causes of Unscheduled Maintenance
Several factors can contribute to the need for unscheduled maintenance on diesel generators. Understanding these common causes can help operators anticipate potential issues and take proactive steps to prevent unplanned downtime. Some of the most common causes of unscheduled maintenance include:
1. Fuel-related issues: Contaminated fuel, fuel leaks, or improper fuel storage can lead to fuel system problems that affect the performance of the diesel generator. Fuel filters may become clogged, injectors may malfunction, or the engine may experience fuel starvation, resulting in engine shutdowns.
2. Cooling system failures: The cooling system is essential for regulating the temperature of the diesel engine and preventing overheating. Cooling system failures, such as leaks, blockages, or pump malfunctions, can lead to engine overheating and potential damage to critical components.
3. Electrical system faults: Problems with the electrical components of the generator, such as wiring issues, faulty connections, or malfunctioning sensors, can cause electrical failures and disrupt the generation of power. Electrical system faults may result in voltage fluctuations, short circuits, or complete power loss.
4. Battery issues: Diesel generators rely on batteries to start the engine and provide backup power in case of an outage. Battery issues, such as low voltage, corrosion, or poor connections, can prevent the generator from starting or cause it to shut down unexpectedly.
5. Mechanical wear and tear: Continuous operation and normal wear and tear can lead to the deterioration of mechanical components, such as belts, bearings, gaskets, and seals. Over time, these components may fail, leading to breakdowns and the need for unscheduled maintenance.
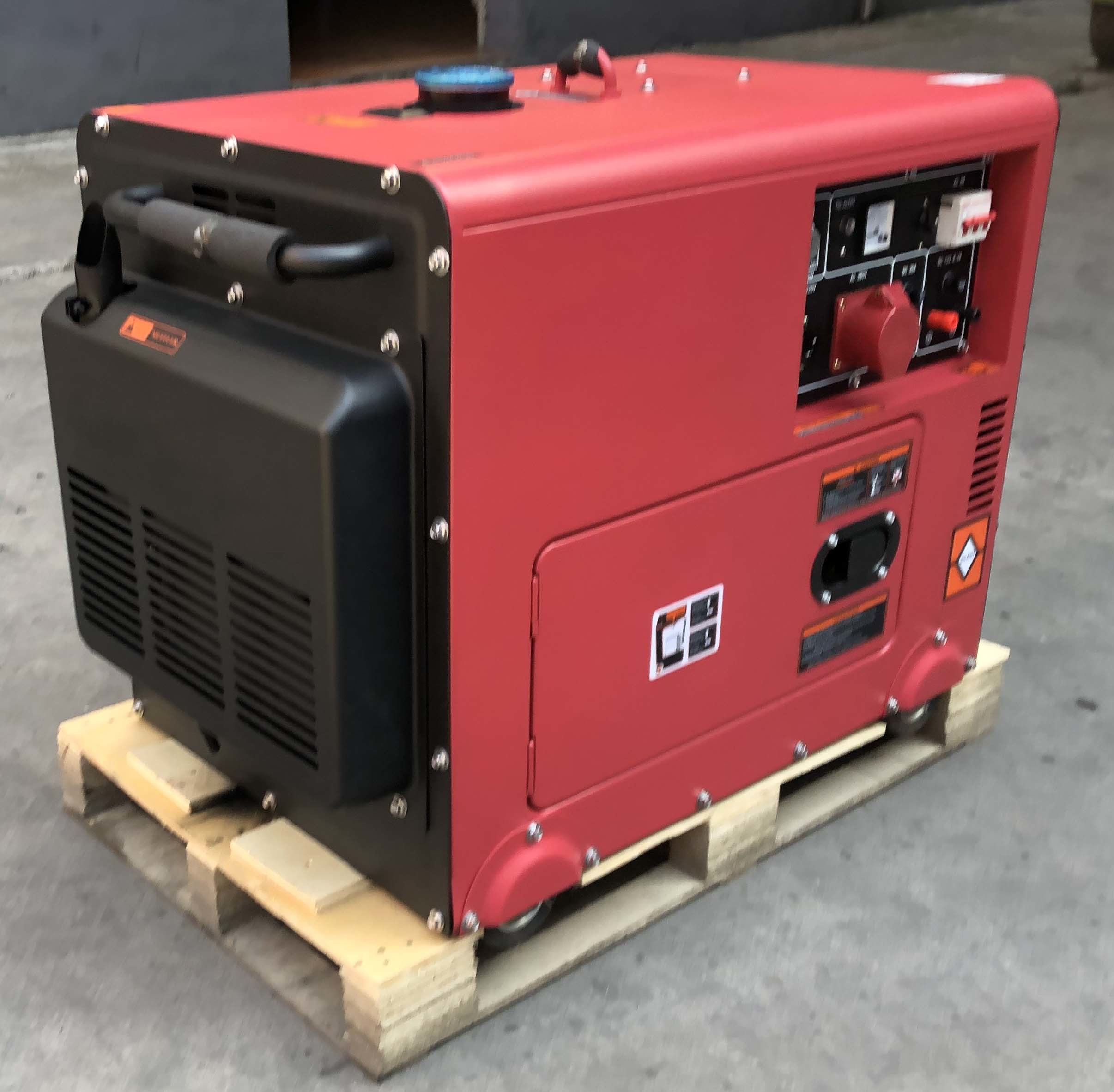
Effective Strategies for Managing Unscheduled Maintenance
To effectively manage unscheduled maintenance for diesel generators, operators can implement the following strategies to minimize downtime, reduce repair costs, and ensure reliable performance:
1. Regular monitoring and inspections: Monitoring the operating parameters of the diesel generator, such as temperature, pressure, fuel levels, and battery voltage, can help detect early signs of potential issues. Regular inspections of critical components, such as filters, belts, hoses, and connections, can identify wear and damage before they lead to failures.
2. Prompt response to alarms and alerts: Diesel generators are equipped with monitoring systems that detect abnormal conditions and trigger alarms or alerts. Operators should respond promptly to these notifications to investigate the cause of the issue and take corrective action before it escalates into a major problem.
3. Spare parts inventory and emergency kits: Maintaining a stock of essential spare parts, such as filters, belts, gaskets, and sensors, can expedite the repair process during unscheduled maintenance. 500kw diesel generator for rural electrification should also have emergency kits with tools, lubricants, and diagnostic equipment on hand to quickly address unexpected issues.
4. Training and skill development: Providing training for operators and maintenance personnel on the proper operation, maintenance, and troubleshooting of diesel generators can improve response times and ensure that issues are addressed effectively. Developing technical skills and knowledge can empower staff to perform diagnostic tests, identify problems, and implement solutions efficiently.
5. Collaboration with service providers: Establishing relationships with qualified service providers and authorized dealers can provide access to technical expertise, specialized tools, and genuine replacement parts for diesel generators. Collaborating with experienced professionals can help resolve complex issues and ensure that unscheduled maintenance is performed according to manufacturer recommendations.
6. Documentation and reporting: Maintaining accurate records of maintenance activities, service history, repairs, and inspections can help track the performance of diesel generators and identify recurring issues. Documentation can also serve as a reference for troubleshooting, warranty claims, and compliance with regulatory requirements.
Case Studies and Best Practices
To illustrate the importance of unscheduled maintenance and highlight best practices for managing unexpected issues with diesel generators, consider the following case studies:
Case Study 1: Contaminated Fuel
A manufacturing plant experienced frequent shutdowns of its diesel generator due to fuel-related issues. Upon investigation, it was discovered that the fuel storage tank was contaminated with water and sediment, leading to clogged filters and injector problems. Pros and cons of owning a 75kW generator implemented a proactive fuel management program, including regular fuel testing, tank cleaning, and filter replacements, to prevent future fuel-related failures. By addressing the root cause of the issue through unscheduled maintenance, the plant reduced downtime and improved the reliability of its generator.
Case Study 2: Cooling System Failure
A data center encountered an unexpected shutdown of its diesel generator during a heatwave, resulting in a critical loss of power. An inspection revealed that the cooling system was not functioning properly, causing the engine to overheat and trigger an automatic shutdown. The data center implemented a cooling system maintenance schedule, including periodic inspections, coolant flushes, and pump replacements, to prevent similar failures in the future. By proactively addressing the cooling system issue through unscheduled maintenance, the data center avoided costly downtime and protected its sensitive equipment.
Conclusion
Unscheduled maintenance is a critical aspect of diesel generator management that requires proactive planning, timely response, and effective troubleshooting. By understanding the common causes of unscheduled maintenance, implementing strategies to manage unexpected issues, and learning from best practices, operators can ensure the reliable performance of their diesel generators and minimize the impact of unplanned downtime. By prioritizing unscheduled maintenance alongside scheduled maintenance activities, operators can optimize the operation, longevity, and efficiency of their diesel generators for years to come.